Top 5 Civil Equipment Hire Problems And Solutions
In a fast-paced and detailed sector such as civil construction, procurement managers and foremen, are challenged with the task of ensuring the correct equipment is always available. Now more than ever before, businesses are looking to optimise the way that they operate with their suppliers. Plant hire included. However, with our 25 years of experience in navigating the complexities of civil equipment hire, we’ve put together the top 5 problems and solutions to help.
So where do we start? Well, let’s begin by understanding the importance of solving these problems and how they will affect you in your role.
The importance of solving common problems related to civil equipment hire
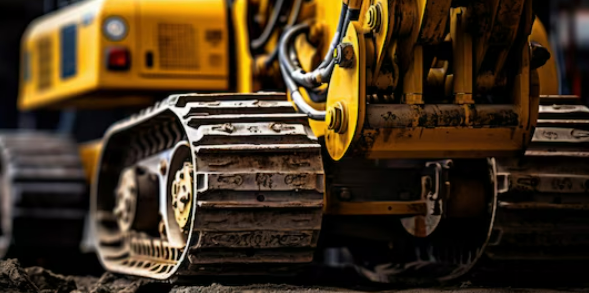
If you are involved in the civil construction industry, you’ll be no stranger to the stresses that come with purchasing or ordering equipment. Hurdles such as budgets, availability and reliability can have a direct impact on the progress of a build. Therefore, if you have encountered any of these challenges before, you can certainly appreciate the significance of using the right civil equipment hire service.
Using the right civil equipment hire has a huge number of benefits in doing so. Remember that every decision that a business chooses can make or break a project. Let’s have a close look at them.
Flexibility
Imagine having the freedom and flexibility to scale up or down your fleet size to meet your requirements. Ideal if you are operating across multiple different sites at one time or if you need to work closely with your budget. Working closely with the right civil equipment supplier can provide the flexibility and inventory management to suit your own needs, without overstretching.
Cost efficiency
Opting for equipment hire these days allows you to be far more efficient with your funds. Instead of purchasing large equipment, which requires huge investment, you can achieve the same outcome, whilst easily distributing additional funds to other parts of the business. In addition, with clear costings from your supplier, you will have no nasty surprises. Always check the fine print so you don’t get caught out.
Access to state-of-the-art equipment
Leveraging the latest innovations to aid you in enhancing productivity, efficiency and meeting emissions targets can play a huge benefit on its own. Staying ahead of the industry will only allow businesses to optimise their spending when it comes to involving a 3rd party member. Partnering with a reputable civil equipment supplier ensures you have access to a well-maintained fleet with up-to-date safety standards. Thus, leading to the reduced chance of breakdown and on-site accidents occurring.
Support throughout projects
The equipment quality is only half of the decision when choosing a reputable civil equipment hire supplier. Downtime can lead to unwanted delays and overspending, therefore partnering with a business that will offer you the levels of onsite support you need is essential. Even vigorous testing is conducted on earthmoving equipment before it arrives on site. What happens thereafter can cause problems. A leading provider will be able to offer you technical support or fast equipment replacement, should you come across any bumps in the road. Overall, this will increase your overall productivity and maximise your efforts.
The top 5 civil equipment hire problems

Now that we’ve highlighted the benefits of using the right civil equipment hire services. Let’s look at the most common problems you will, no doubt, navigate when being involved in the decision-making process of hiring equipment.
Availability
As business decision-makers, one of the most significant problems is ensuring there is availability of the equipment you need to meet the task at hand. Delays in equipment delivery and acquisition can be detrimental when it comes to keeping on track.
Cost management
Next is the management of hire costs within your budget constraints. Hire rates, fuel, delivery, cleaning and additional insurance fees may all need to be accounted for. Unexpected fees such as equipment damage costs can quickly escalate and can apply pressure.
Quality and suitability
Thereafter is the quality and suitability of the equipment you are hiring. As decision-makers within your business, you need to ensure the machinery is “fit for purpose” along with meeting your project requirements. A mismatch or inadequacy could lead to a compromise in safety and efficiency.
Competency of staff
The efficiency and competency of your staff can raise issues when it comes to choosing to hire. Even though hiring civil equipment doesn’t require the production of a licence, your business will still be liable for its use. Incompetent operators can jeopardise project safety and are more likely to damage imported equipment.
Maintenance and downtime
Proper maintenance is essential to keeping earthmoving equipment moving and minimising downtime. With the many other challenges involved with civil equipment hire, coordinating or addressing unexpected breakdowns can lead to huge productivity loss.
Solutions to tackle civil equipment availability
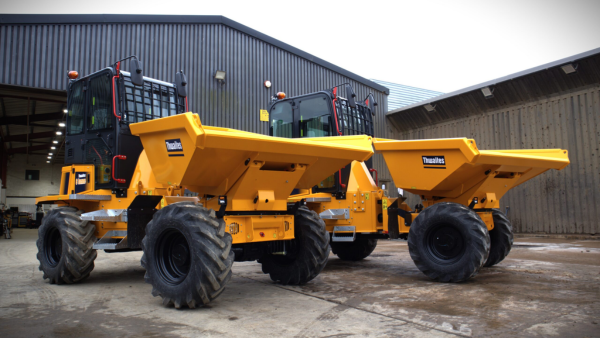
In the fast-paced world of construction having great access to a vast range of equipment can levitate the pressures of meeting targets. To navigate the hurdle of availability, implementing the best practices is crucial. Here are some of the best solutions to help.
Clear communication
Clear effective communication between you and your supplier is essential. This may require scaling out timelines for them to deliver the required equipment to meet your needs. It is best practice to be direct and upfront to minimise any misunderstandings. Clear communication also allows you to proactively address any issues should they arise during your project. We highly recommend a document paper tail be created to align with your project milestones.
Strong relationships
Building long-term relationships with suppliers is key to earning trust and access to in-demand equipment during peak season. These relationships can further grant access to exclusive discount rates for long-term projects and loyal clientele. Therefore, allowing you to operate far more efficiently and make savings throughout a build. Transparency will allow you to effectively communicate your goals and build stronger connections with your supplier.
Leverage data analysis to forecast
The analysis of data can only be determined after a period of hire. However, having access to this vital information can allow you to forecast your requirements in the future. Use your strong relationship with your supplier to leverage this data and understand your availability requirements to avoid any project delays in the future.
By implementing these practices, you can proactively tackle civil equipment availability challenges and optimize your construction project’s success. Now let’s take a look at the solutions to cost management.
Solutions to tackle cost management with civil equipment hire
Cost management is essential in the civil engineering world. Effective budgeting, transparency and balancing operating needs are required to guarantee success. But how do we achieve that? Well, here are some actionable strategies that you can use to aid you in your cost management with civil equipment hire.
Conduct cost analysis
Conducting a detailed analysis of the equipment you use is critical to understanding the “true cost.” That doesn’t mean just the equipment. You are going to need to know, fuel consumption, delivery or moving rates per mile, insurance costs, and potential downtime, per machine/day. Having a clear understanding and analysis of all the potential costs will allow you the easily tackle your cost management with any civil equipment hire company.
Negotiate long-term rates
Negotiation is a powerful tool to leverage, especially if you intend to hire equipment long-term. Short-term civil equipment hire doesn’t normally adopt any discounts, however, loyalty and reliability will no doubt, open up access to more favourable rates over time. It is always worth exploring these potential options with your existing or prospective to aid you in your cost management.
Explore cost-effective alternatives
You should always consider other cost-effective alternatives if for some reason the equipment you require is unavailable. Working closely with your provider will enable you to quickly find solutions. This, in turn, provides a cost-effective solution to the optimising cost management. Remember that delays in decision-making can have a knock-on effect across the project you are responsible for.
To conclude, by conducting cost analysis, negotiating long-term rates and working closely with your supplier, you can easily grasp most of the cost management problems that may occur when hiring equipment. Now we’ll take you through the solutions to tackle civil equipment quality.
Solutions to tackle civil equipment quality
Tackling civil equipment quality can be a long and daunting task, especially when assessing potential business prospects. However, to maintain safety standards along, as well as the levels of efficiency and productivity you wish to meet, there are solutions to ensure you make the right choice the first time. Let’s explore these together.
Conduct thorough assessments of machinery
Before committing to any equipment hire agreement, conduct a thorough assessment of the equipment you will be hiring. What is the quality like? Why may the supplier choose a particular manufacturer? Inspect all machinery for signs of wear, and defects and ensure it meets the safety regulations you must adhere to. We’d highly recommend that you partner with a supplier that takes a huge amount of pride in prioritising equipment maintenance and quality control standards.
Verify equipment specifications
To ensure your teams don’t run into any hiccups on the ground, always verify the specifications of the equipment from your supplier. Not only are they project-specific, but they also comply with industry standards. Specifications such as capacity, weight, dimensions, lifting weights and emissions outputs, should all be considered. If deemed necessary, you can also request copies of documentation or certification of the equipment before placing an order.
Prioritize businesses that support
During your vetting process, you should consider prioritizing suppliers that have a large focus on support. Establish proactive maintenance schedules to effectively reduce the risk of breakdown and downtime of the machine. This is essential when using civil equipment on long-term hire. Partnering with suppliers that offer this service will help your business avoid any potential risks from escalating.
By implementing these solutions, you can effectively tackle civil equipment quality challenges and ensure that your construction projects are equipped with reliable, high-quality equipment. Now let’s take a look at the solutions linked to the competency of staff.
Solutions to tackle competency of staff with civil equipment hire
The competency of staff is vital to maintaining a productive and safe worksite. Of which, as we have already highlighted, you will be responsible for. Therefore, it is essential to introduce measures to protect them when using civil equipment hire. Here are some easy actionable solutions that can quickly help you navigate this issue.
Certification and licensing
Ensure that all your staff hold and are competent in using the latest machinery available with civil equipment hire companies. You must adhere to the HSE regulations and wherever possible facilitate the attainment of this training. Additionally, organise periodic training dates to continually boost operator safety. WHC Hire highly recommends using Vally Plant training for on-site civil equipment training.
Operated plant equipment
Another solution to tackling staff competency with civil hire is to explore to possibility of using operated plant. This process includes the addition of a skilled operator with your civil hire equipment. Whilst the cost is dearer, this process can be used effectively if budgeted for in advance. It is worth noting that not all civil equipment hire providers will offer this service. Nevertheless, it is certainly a consideration to have in your arsenal, be the situation arises.
So in short, the solution to tackle this issue is to ensure that all your staff are adequately trained to use the equipment you want to hire. Some insurance companies will not cover your business without being able to produce certificates of competency. Alternatively using an operated plant can work where your budget allows. We’ll now move on to covering the solutions for the last of the 5 top problems with civil equipment hire. Maintenance and breakdown.
Solutions to maintenance and breakdown problems with civil equipment hire
Equipment breakdowns are inevitable in a machine’s lifetime. However, having adequate support behind you from your provider can help avoid any nasty unwanted delays. In this section, we will highlight some simple ways to mitigate the potential of maintenance and breakdown problems occurring whilst using civil equipment hire.
Vet of your prospect
We’ve already discussed vetting out your prospect in a previous section, however, we cannot highly recommend this enough. During your information gathering stage, get the know the supplier closer, find out exactly what equipment they use, conduct independent research of individual items of machinery, and lay down your needs to see if they can be met. Correct prospecting will allow you to understand to protocols that occur when a breakdown occurs, or maintenance is required. Some of the questions you may wish to consider are, “What is your response time?”, “How often do conduct maintenance of machinery?”, “What happens if the equipment fails?”
Scheduling maintenance on long-term hire
Scheduling maintenance while on long-term hire can play to your business strengths. Aim to try and schedule these when the machinery is least likely to be operating and regularly. In turn, this will ensure that the equipment your teams are using day in and out works to their optimum and delivers results that match your project timeline.
Therefore, to conclude, the most effective solutions to maintenance and breakdown problems with civil equipment hire are to vet out your supplier and regularly schedule maintenance of the equipment. By conducting these easy solutions, you can illuminate the most common issues when hiring civil equipment.
Conclusion
In conclusion, navigating the complexities of the civil equipment hire can be difficult, however, but implementing some of the surgeries we’ve raised, should make your life much easier. We hope that this article has helped provide valuable insight into overcoming the challenges you face on a day-to-day basis in the civil sector.
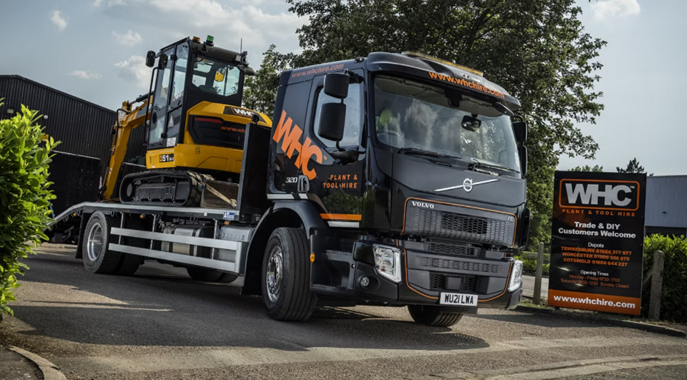
Are you ready to take your civil engineering projects to the next level? Check out a wealth of construction hire insights in our resource vault, to help maximise every penny you spend on plant and tool hire. Alternatively, speak to one of our team who would be delighted to help you further. See our full catalogue here.