Solutions To Common Plant Hire Issues.
Hired plant comes with its potential downfalls, as the same in every industry. There is no fooling it. Each person’s experience is sure to be different from plant hire companies, as we all have dissimilar needs and wants. Nevertheless, there are certainly some common issues with hired plant that we want to help you avoid. This resource is dedicated to highlighting those potential issues and how to steer clear of any disappointment.
Choosing the right plant hire company to partner is a very timely task. It is an easy solution to just pick the first company you see without doing your research. Why do many take this option…? For convenience. Surely no one wants to risk their company’s reputation for convenience, right? This brings us to our first common issue, which is not working with a reputable company.
Working With A Reputable Company
One of the most common issues that businesses suffer from is not working with a reputable company. The way that business is spoken about is a good indication of the previous experience that others have had with them. It is highly likely that in today’s day in age, one of the preferred ways to identify prospects is to see their online reviews.
There are plenty of different platforms that host online reviews for plant hire companies. The most influential being the likes of 3rd party review platforms. Google, Trustpilot, Yell.com etc. Why? Well, if you base reviews just on what their website says, it’s likely you might not get the whole truth. Nevertheless, when investigating, it is worth checking that your prospect is registered with the CPA (Construction Plant Hire Association) https://www.cpa.uk.net/
“The Construction Plant-hire Association (CPA) is the leading membership and representative body for construction plant-hire in the UK. Established for 80 years, we now have in excess of 1,800 Members, ranging from owner operators with a single machine, right through to the largest companies in the industry, with hire fleets of thousands of machines. “
This, along with other governing body accreditations are always desirable when choosing your prospect. A reputable company will be glad to answer any questions you have and add to your knowledge about the plant. They will be dedicated to their customers and want to ensure you get a good service.
This then brings us to the next issue that businesses have, which is the quality of the equipment supplied.
Quality Of The Equipment
Now that you have done your reputation checks, next, assess the equipment that they offer. How do you do this you might ask? Before assessing the cost, the first port of call is to see the machinery first-hand. Pay the supplier a visit and ask to see the machinery that they offer. Sometimes when basing your judgement of photographs on the internet, you can start to paint a misdirected image of the state of the equipment.
Some of the most important questions you need to answer are:
- Is the equipment fit for purpose?
- Is the equipment in good condition?
- What is the age of the equipment?
- Will the quality of the equipment enhance or affect your own reputation?
If you are working with a reputable hire company, as we have previously discussed, they will be more than happy to show you firsthand the quality of the equipment. If you get any friction by asking to assess the machinery yourself, this could impose a red flag on your decision.
In addition, it is important that your project will benefit from the machinery that you are looking to hire. Is it big enough? Are there alternative options? What is the quality of those options? If you are not too sure about the selection process of the equipment, then your supplier should be able to point you in the right direction. You must ensure that before committing that the machinery is suitable, otherwise, you could be shedding out for machinery you simply just won’t use.
So far, we have avoided choosing an unreputable supplier and now assessed the quality of the equipment. The next issue to avoid, which is one of the latest trip hazards in the plant hire industry is cost.
Cheap Hire Rates
One of the biggest deciding factors in avoiding issues with hired plant, is to avoid the cheap hire rates. Why? Ever heard of the term “if it sounds too good, it probably is”? Well, the truth is quite real within the hired plant industry.
Cheap hire rates are a clear red flag for the possible outcomes:
- Hidden costs involved with your hire.
- Old equipment that will not be suitable or even safe.
- Ill-maintained equipment that could cause a safety hazard.
- Poor support system when hiring in case something goes wrong.
- Cowboys, trying to undercut the market for a quick sale.
During your assessment of the supplier’s equipment, you will start to understand the value of the service that you get for your money. Nevertheless, one clear correlation is that most governed hired plant suppliers to charge a similar rate (within a percentage of each other).
To avoid any issues when using the hired equipment, it is best to choose a supplier that:
- Is transparent with its costs, including if there is VAT involved.
- Uses new low-hours equipment that is in good working condition.
- The machinery is maintained by qualified in-house engineers that work for the supplier (Not contractors).
- Offer a breakdown and replacement service if something is to go wrong.
Since we have not covered all of the grounds of the selection process of your supplier, we now need to observe the issues that can be avoided during the acquisition of the equipment and during use.
Carrying Out Risk Assessments
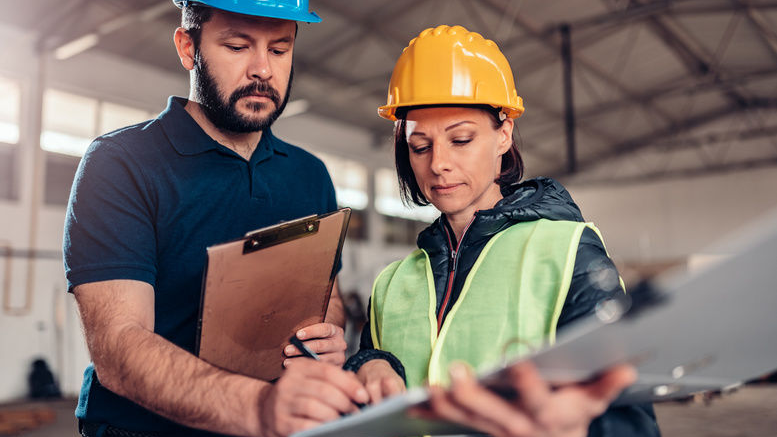
When using hired plant on a project, it is important that you involve the machinery in your risk assessment. This information must be shared with everyone involved. Resulting in everyone being aware of what equipment will be arriving, when and for what purpose. This can allow you and your team to be prepared and allow you to safeguard others. For example, members of the public.
Throughout your risk assessment should have a designated place where the machinery can be delivered, maintained, and stored if required. Doing so will minimise the risk of any issues such as
- Risks that could occur during unloading the machinery.
- Risk of the machinery being tampered with.
- Risks of the machinery being stolen.
- Risk of not being able to access the machine to perform daily checks before operation.
Prior planning for the delivery of hired plant can make all the difference. This also includes not allowing unauthorised or untrained staff to use the machinery. All staff should be trained to use the hired equipment for several reasons.
Void insurance- Unauthorised or untrained operators of hired plant equipment can avoid the insurance policy of the machinery while on hire. More so, the employee’s liability if something was to go wrong.
Damage to hired plant- Inexperienced operators increase the chance of damaging the machinery that you have hired. This could cost a claim on your hired insurance or leave you with a costly bill.
Health and Safety breach- Staff that wish to operate a piece of hired plant on a building site must hold an NPORS certificate. Failure to do so is a breach of Health and Safety and in turn will leave you and your business open to financial penalties.
Making Sure The Hired Plant Is Safe
It is very common that when we hire machinery; we are more desperate to get the equipment where we need it to be to start work. Of course, time is money. But it is crucial to take your time assessing the equipment during handovers to ensure everything is working correctly.
One way to increase your chances of having safe equipment to use is to use a supplier that has a track record for health and safety. A globally-renowned organisation that promotes the highest levels of health and safety in the workplace is RoSPA.
Choosing a plant hire supplier that has a proven track record of safety in their equipment will avoid you from having any nasty accidents. Nevertheless, it is crucial that you still check the machine, especially if it is delivered to you.
When plant equipment is delivered by your supplier, you will have time the check the machine over before accepting. If for any reason, you are unsatisfied with the quality and state of the machinery, then you should not accept it. This is also a great time to familiarise yourself with the equipment as unless you have hired the exact same machine before, chances are, that the control and features will be different.
Some machines may require a security pin code to use them. This unique code will be given to you when receiving the machine. During your handover, you should ask the supplier for the correct input entry procedure. Incorrect entries lead to the equipment becoming locked. Here is an example of how to use a keycode ignition.
How WHC Hire Services Can Help You Avoid Common Issues With Plant Hire?
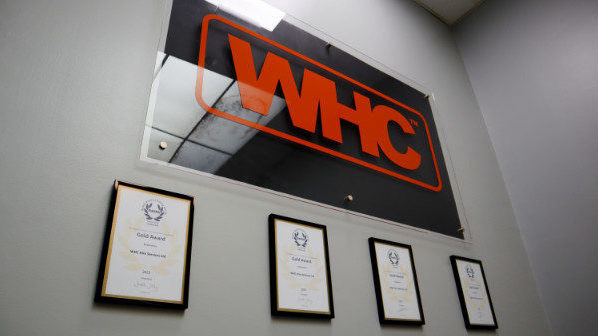
With a wealth of experience, WHC Hire Services provides one of the most advanced fleets of plant hire equipment on the UK market. We are committed to our customers and their needs, leading to the investment of millions of pounds every year to keep our fleet young and low hours. Awarded RoSPA gold medal winners, we make it our duty to ensure that all our staff and customers go home safe at the end of the day. This is reflected in the detailed processes and procedures that we have established over 25 years of working in the plant hire trade.
Need plant hire from a trusted, honest, and reputable supplier? Give our friendly team a call to find out how we can help. 01684377977
Or
View our online catalogue of machinery available from our three depots in Worcester Gloucestershire and the Cotswolds.