Plate Compactors for Asphalt: Essential Tips for Civil Engineering Start-Ups
Striving for that consistent professional finish with every civil engineering project? If you’re finding yourself lagging behind, outdated machinery could be the culprit. Let’s guide you through evaluating your plate compactor choices for asphalt tasks. It’s all about keeping productivity at its peak while maintaining the high standards you’ve set. Whether you are new to civil engineering, or a seasoned professional, adopting the latest innovative equipment can save you time and stress out in the field. To start, let’s take a close look at understanding plate compactors and why they are top dogs when it comes to laying asphalt.
Understanding plate compactors for asphalt
Plate compactors are a popular piece of construction equipment used by civil engineering professionals to compact materials such as asphalt. They do this through their large, heavy plates forged from steel, vibrating at high speed. The force of the vigorously vibrating plate, forces the movement of the particles of the material closer together to eliminate air pockets and moisture. Plate compactors are popular to use on the 3 common asphalt groups used on 95% of all UK roads. These are asphalt concretes, hot road asphalts and stone mastic asphalts.
Types of plate compactor for asphalt
There are commonly three different types of plate compactors leading civil engineering businesses will use on asphalt projects. These are:
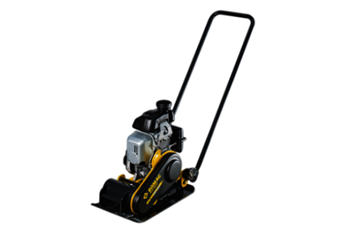
Small, lightweight compactors, offering a compression rate of around 10KN. Suitable only for small asphalt tasks using hot or cold mix for potholes, driveways and pathways. These compactors can only be used in a forward motion.
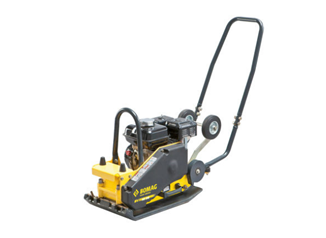
A large plate compactor offers a similar compaction rate, but over a wider area. Meaning more can be conducted at one time. It is worth noting these machines are around 25% heavier than their smaller alternatives. Nevertheless, these machines are suitable for hot or cold mixes on potholes, driveways and pathways, but only offer a forward motion.
Forward-Reverse Plate Compactor
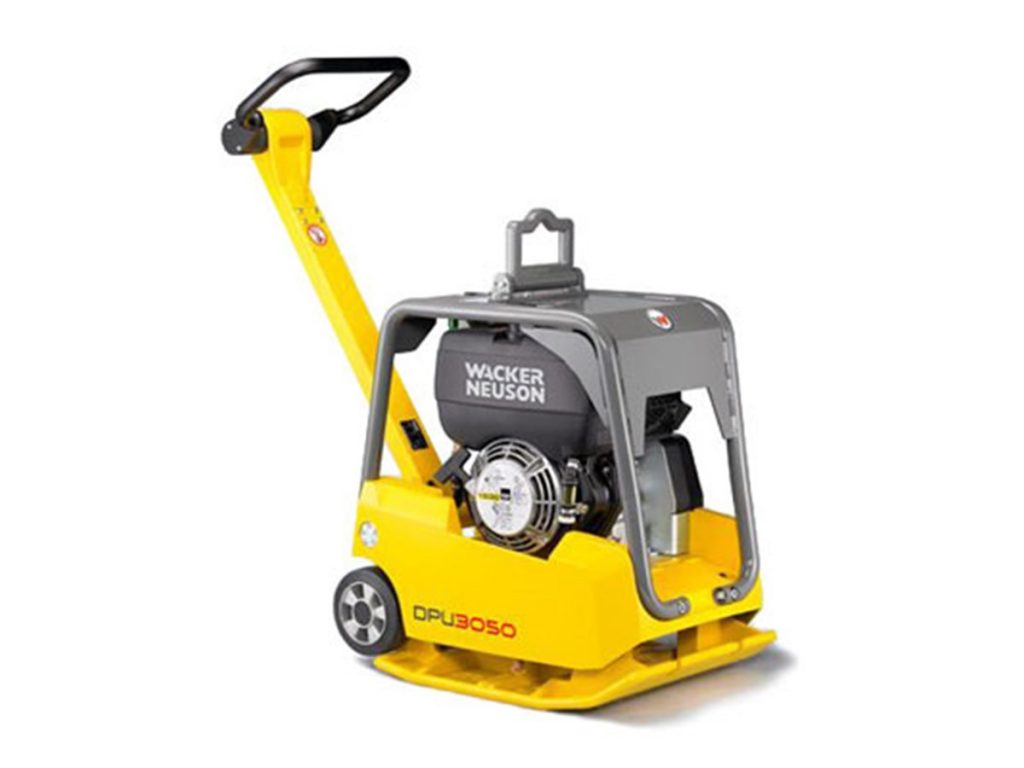
The largest hand-operated machine on the market is the forward-reverse plate compactor. These heavy machines weigh in at double the amount of a large plate compactor, providing sufficiently more compression force of 25KN. Their forward and reverse capabilities also allow continuous pressure to be applied across the working area without having to turn the machine. This equipment is ideal for hot or cold mix pathways, driveways, potholes, utility ducting and more.
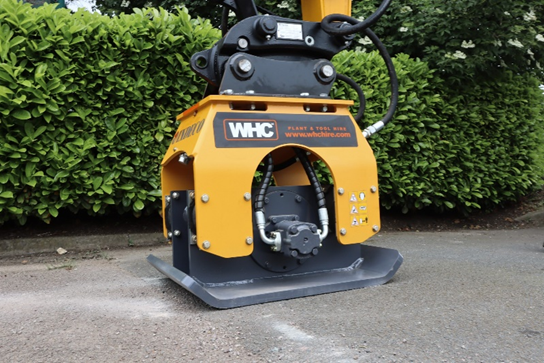
The hydraulic plate compactor is one of the latest additions to the market. These machines use the auxiliary hydraulic output of an excavator to function. They offer the largest compression rates from 39KN of their category (Machine size dependent). Therefore, they are by far the most efficient. These compactors can be moved in all directions.
How do they work?
Plate compactors feature a vibrating plate which is powered by a hydraulic or petrol engine that vibrates rapidly when turned on. As the plate moves across the asphalt the vibrations help to compact the material underneath, creating a stable, sleek finish. In using a plate compactor, you’ll ensure a durable, professional, aesthetic result.
Why should civil engineers start ups use a plate compactor for asphalt?
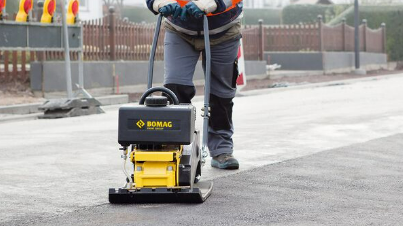
Proper compaction is paramount when working with asphalt surfaces. Here are the key reasons why incorporating a plate compactor into your asphalt projects is essential:
- Enhanced durability and longevity: Plate compactors ensure that the asphalt surface is thoroughly compacted, eliminating voids and air pockets. Resulting in a denser and more stable surface that can withstand the environmental stresses of its application. With proper compaction, your asphalt surface will exhibit greater durability and longevity, reducing the need for frequent repairs or replacements.
- Cost savings on maintenance: Investing in a high-performance hired plate compactor can lead to significant cost savings over time. A well-compacted asphalt surface will result in fewer issues such as cracking, rutting, or potholes. By reducing the occurrence of these issues civil engineers can concentrate on their next task rather than going over old ground.
- Prevention of uneven surfaces: Plate compactors ensure uniform compaction across the entire surface, eliminating low spots and irregularities. This results in a smoother and more visually appealing asphalt surface, enhancing the overall quality and appearance of your project.
Common Mistakes to Avoid
While plate compactors are incredibly valuable tools for asphalt projects, it’s essential to use them correctly to avoid common issues. Here are some mistakes to be aware of:
- Over-Compacting: Excessive compaction can be just as detrimental as insufficient compaction. Over-compacting can lead to the asphalt mix cracking and deforming over time. It is crucial to follow manufacturer’s guidelines and compaction specifications to achieve the optimal density without causing complications.
- Surface Preparation: Proper surface preparation is essential for achieving the best compaction results. Failing to prepare the surface correctly by removing debris, levelling uneven areas, and addressing moisture, will affect the compaction process. Take time to inspect and prepare the surface before introducing your asphalt.
- Using the Wrong Type of Compactor: Using the wrong type of compactor or selecting one that is too small can result in later complications. Choosing the right plate compactor is essential to maximise your productivity and achieve the high standards your business strives for.
By understanding the benefits of proper compaction and avoiding common mistakes, you can maximise the effectiveness of plate compactors in your asphalt projects, ultimately achieving superior results and minimising future maintenance needs.
Choosing the right plate compactor for asphalt tasks
So, is your civil engineering business selecting the right plate compactor for your asphalt tasks? Well to help assess your equipment selection, you should consider the following factors to get your started:
Size and scale of the project
The size and complexity of your project is always a hurdle to firstly consider. For smaller, tighter projects, you may want to consider a small plate compactor which will offer the logistic flexibility and operation for such tasks. Whereas, larger projects can benefit from larger equipment to increase efficiency when your teams are running against the clock.
Compactor size and weight
Being mindful of the size and weight of your compactor is essential when choosing the correct machinery. For thicker layers of asphalt, always opt for equipment that can penetrate deeper to achieve your required compaction rate without causing complications. However, it is essential to note that the compactor is manageable for your team and doesn’t cause unwanted delays.
Recommended Plate compactor brands for asphalt
Top Models and Brands
We’d highly recommend exploring reputable equipment rental companies offering a range of plate compactor models from trusted brands. Tool hire providers often stock top-quality plate compactors from brands like Wacker Neuson and Bomag, ensuring reliability and performance for your asphalt projects.
Vetting a supplier
Seek recommendations and reviews from other civil engineers or industry professionals who have experience hiring equipment from potential candidates. In addition, researching your prospects online can provide a closer insight into their quality and service. Review sites such as Google My Business and Trustpilot are some of the most trusted digital review platforms on the market. For more information on how to choose the right supplier, check out this article: How To Choose The Right Equipment Hire Company Near Me?
Tips for Using Plate Compactors on Asphalt
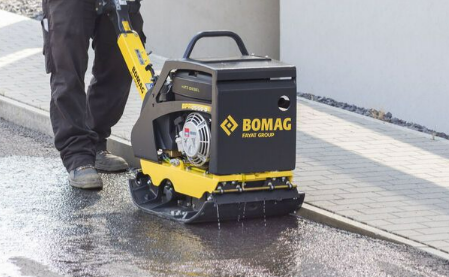
Proper use of plate compactors is essential for achieving a quality finish for your asphalt task. These expert tips will help you maximise your productivity and efficiency when hiring one of these machines.
Initial Steps
- Site Inspection: Before compacting inspect the surface for any debris, uneven areas, or potential hazards. Clear the area of any obstacles that may interfere with the compaction process.
- Surface Cleaning: Keep the working area clean. This will avoid any contaminants affecting the asphalt and the compacting process. This could be things such as unwanted dirt, rocks, concrete etc.
- Moisture: Check the moisture content of the asphalt surface to ensure it is within the recommended range for compaction. Incorrect moisture levels can lead to poor bonding between layers.
Compaction Process
- Pre-Start Checks: Ensure the plate compactor is set up correctly. This includes checking fuel levels, oil levels, and inspecting the compactor plate for any damage or wear. Using faulty equipment can lead to poor results.
- Compacting: Begin compacting at the edges of the asphalt surface and work your way towards the centre. Overlap each pass by approximately 1/3 of the plate width to prevent missing any spots.
- Steady Speed: Maintain a steady pace and allow your equipment to do the work for you. Over-compaction can occur if you rush this stage.
For Top Results
- Compaction Patterns: Use a variety of directions and patterns to help achieve a uniform finish. Where possible, keep an eye on your asphalt temperature. The hotter the better to reach optimal compaction.
- Compaction Depth: Adjust your needs to the equipment you are using. Some machines offer larger compacting forces to help accompany thicker asphalt layers. Using a smaller compactor will require thinner, more frequent layers to reach an optimum compaction rate.
Safety
- Personal Protective Equipment (PPE): Wearing the correct PPE is essential to the safety of your team. You should always adhere to the safety information that is recommended by your supplier. These will include safety glasses, hearing and eye protection and steel-toed boots.
- Equipment Safety: Always adhere to the safety guidance set out in the equipment’s operators manual. Ensure that the machinery is in good working order before operating. All faulty equipment should be reported to your tool hire provider.
Maintenance and care of hired plate compactors
If you choose to hire a plate compactor for your civil engineering project, regular maintenance will be conducted by your supplier to ensure longevity and performance. This will include noise and vibration testing. To help you conduct an assessment to avoid any complications, you should address the following before each use:
- Engine: Check the engine’s oil level each time before starting the machinery. This will ensure peak performance when in operation.
- Plate Inspection: Examine the compactor plate for excessive wear and tear. This may include cracks or damage that you should highlight to your tool hire supplier. Insufficient equipment will only lead to project complications.
- Fuel System: Ensure the equipment is fuelled correctly and the fuel system is turned on before operating. Incorrect fuel use can lead to unwanted breakdowns.
- Vibration Exposure: Ensure you have the latest vibration testing results to plan staff exposure throughout use. Remember if you are not doing this already, it is a legal requirement. See more here.
Most common issues: Troubleshoot
Despite their simplicity, some common issues that occur with plate compactors are:
Not Starting: If the machine fails to start. Be sure to check that the fuel valve is open and the choke is on (cold start). On hired plate compactors, do not disassemble the equipment, you should contact your supplier immediately for assistance.
Excessive Vibrations: If the plate compactor suddenly starts excessively vibrating, this could be due to loose components. You should immediately stop work and contact your equipment provider. Unsafe exposure to vibrations can have an irreversible impact on your worker’s health. Get a replacement as soon as possible.
Not Compacting: If your machinery is not compacting, ensure the throttle level is set correctly. Or on hydraulic plate compactors, ensure your flow rate matches the requirements stated in the operator’s manual. If your problem still persists, again get in touch with your supplier.
As we’ve highlighted, these are the most common issues you’ll come across when using a hire plate compactor. It is vital to note that should a problem arise; you should always contact the supplier directly for assistance.
Conclusion
In this comprehensive guide to plate compactors for asphalt, we’ve covered all the essential aspects for small civil engineering start-ups. By understanding the importance of proper compaction, choosing the right equipment, following best practices, and finding a reliable supplier, you can achieve a consistently professional finish for every project. Implementing these insights will enhance the efficiency, safety, and productivity of your asphalt projects.
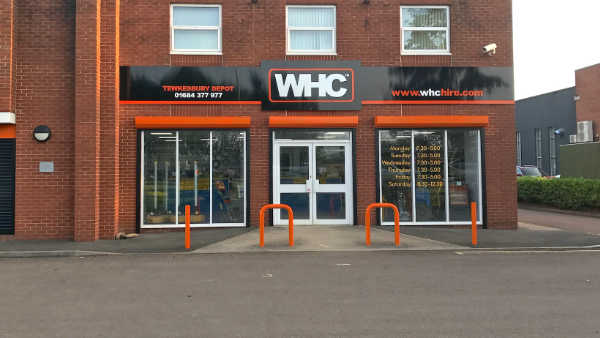
If you’re ready to access world-leading compacting equipment from brands like Bomag and Idenco, reach out to WHC Hire Services today. Our extensive range of compacting equipment is tailored to ensure you deliver a professional finish every time. Browse our selection of compacting equipment or speak to our friendly team on 01684 377977.